By: Alicia Bowers Millinger, Product Marketing Manager – Automation Software, GE Digital
From proactive analysis to guiding operator response, modern alarming technologies use the IIoT’s connected systems layered with new apps to help eliminate alarm noise and confusion while driving the right corrective actions.
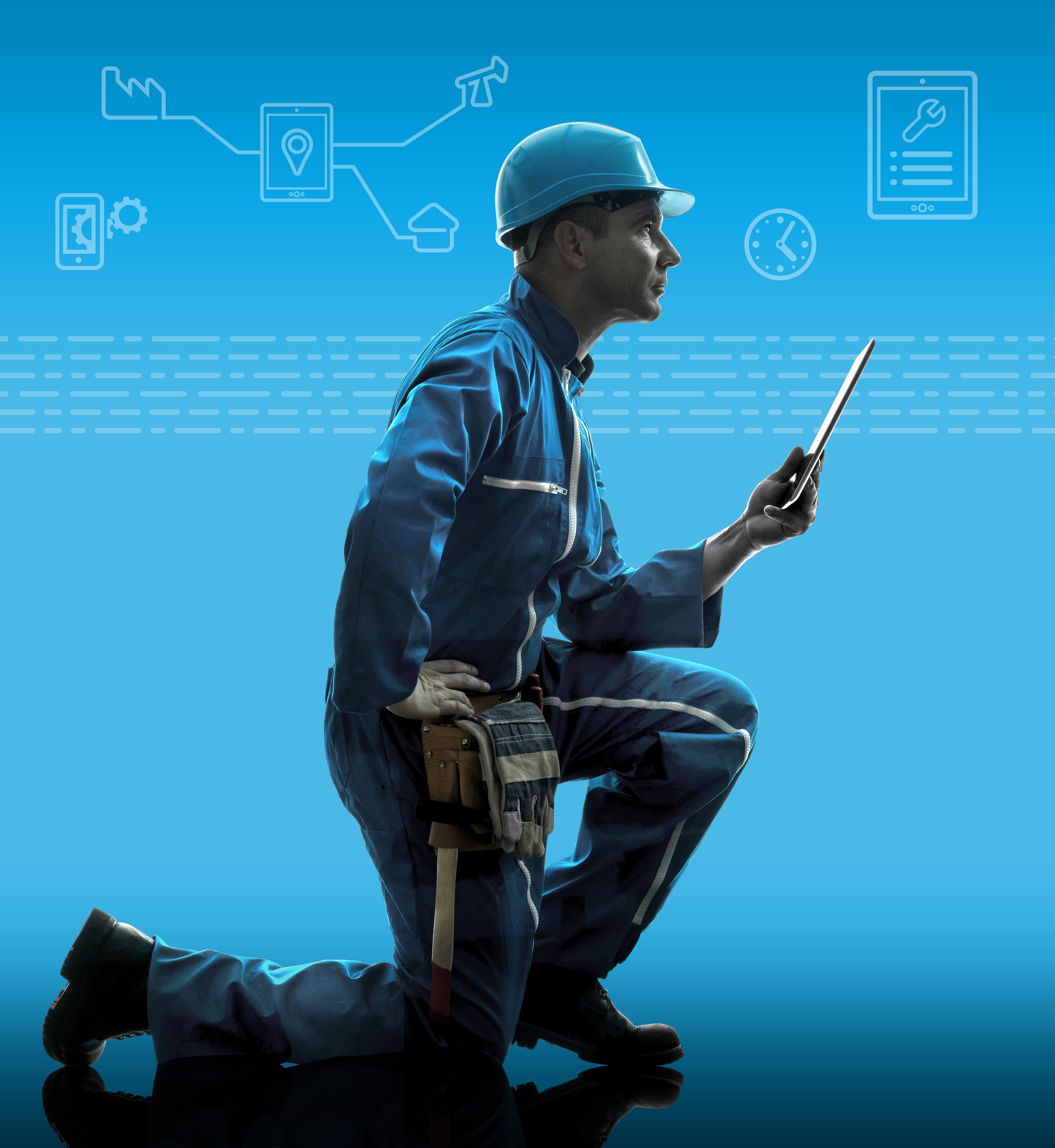 |
With intelligent alarming and the Industrial Internet, systems integrators can configure to send the alarms that matter, when they matter, to the right person. |
What’s the biggest challenge on the plant floor? According to a recent GE survey, managing alarms is still the biggest challenge.
But, today, every organization can manage alarms, and control systems integrators are critical. With intelligent alarming and the Industrial Internet, systems integrators can configure to send the alarms that matter, when they matter, to the right person. Engineers and operators can receive prioritized alerts with instructions, helping them react to and resolve alarms quickly.
An Alarming Situation
According to HMI/SCADA experts at GE Digital, about 75% of all alarms are noise. Many companies want to examine their systems and reduce the number of alarms to improve operator effectiveness. However, this is often an endless cycle. Integrators and in-house engineers typically find new alarms that must be added, while looking to reduce the number of alarms and flags in the system.
Too often, companies are forced to accept that there is a level of noise from alarms, and operators must know what to pay attention to and what does not require action. A problem arises with temporary staff operating machines or new operators coming on board. The temporary or new personnel usually don’t have the experience to filter through the alarm noise and make sense of it.
Additionally, one problem can cause a flood of alarms hitting an operator. Recently working with a major metropolitan area’s transportation team, a proof of concept showed how one problem on a train line triggered an initial alarm, followed by another alarm, followed by ten more alarms, then twenty, and the situation continued. The operators on the trains were inundated with alarms and, in this confusion, unable to identify the real problem.
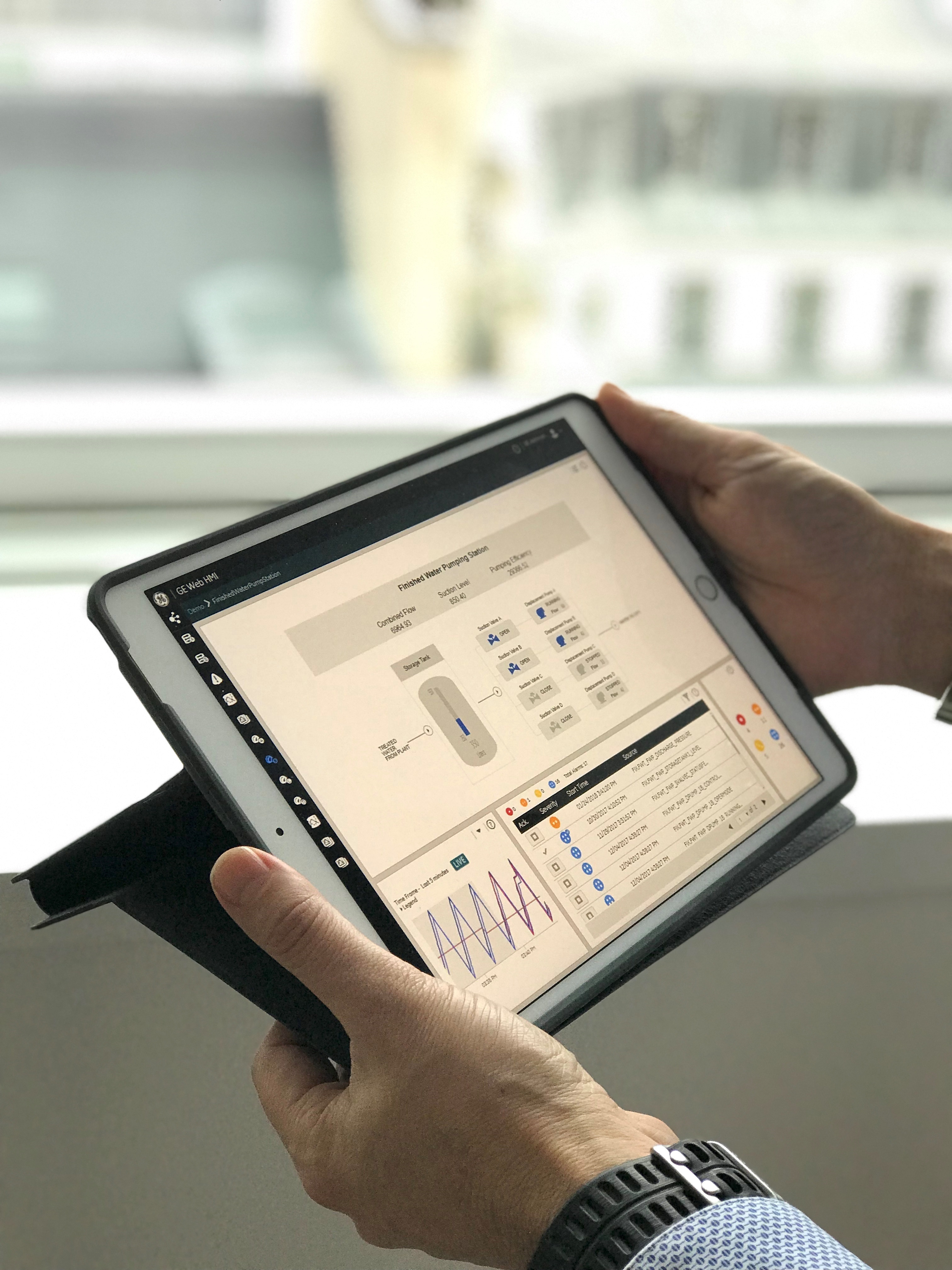 |
Operators can be in a control room or in the field – with instructions going to a mobile device of choice – and deriving intelligence from the raw data. |
Reduce Noise with Machine Learning
In the Industrial Internet world, today’s HMI/SCADA can filter alarms better to increase efficiency. Now, control systems integrators can use machine learning to look at all the raw alarms in underlying systems, determine a root cause, and guide operators through the right corrective actions. Operators can be in a control room or in the field – with instructions going to a mobile device of choice – and deriving intelligence from the raw data.
Machine learning puts traditional alarm rationalization on steroids. HMI/SCADA today, based on the IIoT connected enterprise, can provide full scope alarm management and optimization, facilitating alarm rationalization by providing visibility to all alarms, their respective alarm priority/tier, frequency of occurrence (for a specified period of time), and more, delivering on an alarm philosophy that improves efficiency, reduces unscheduled downtime, and decreases risk.
Be Proactive with Analytics
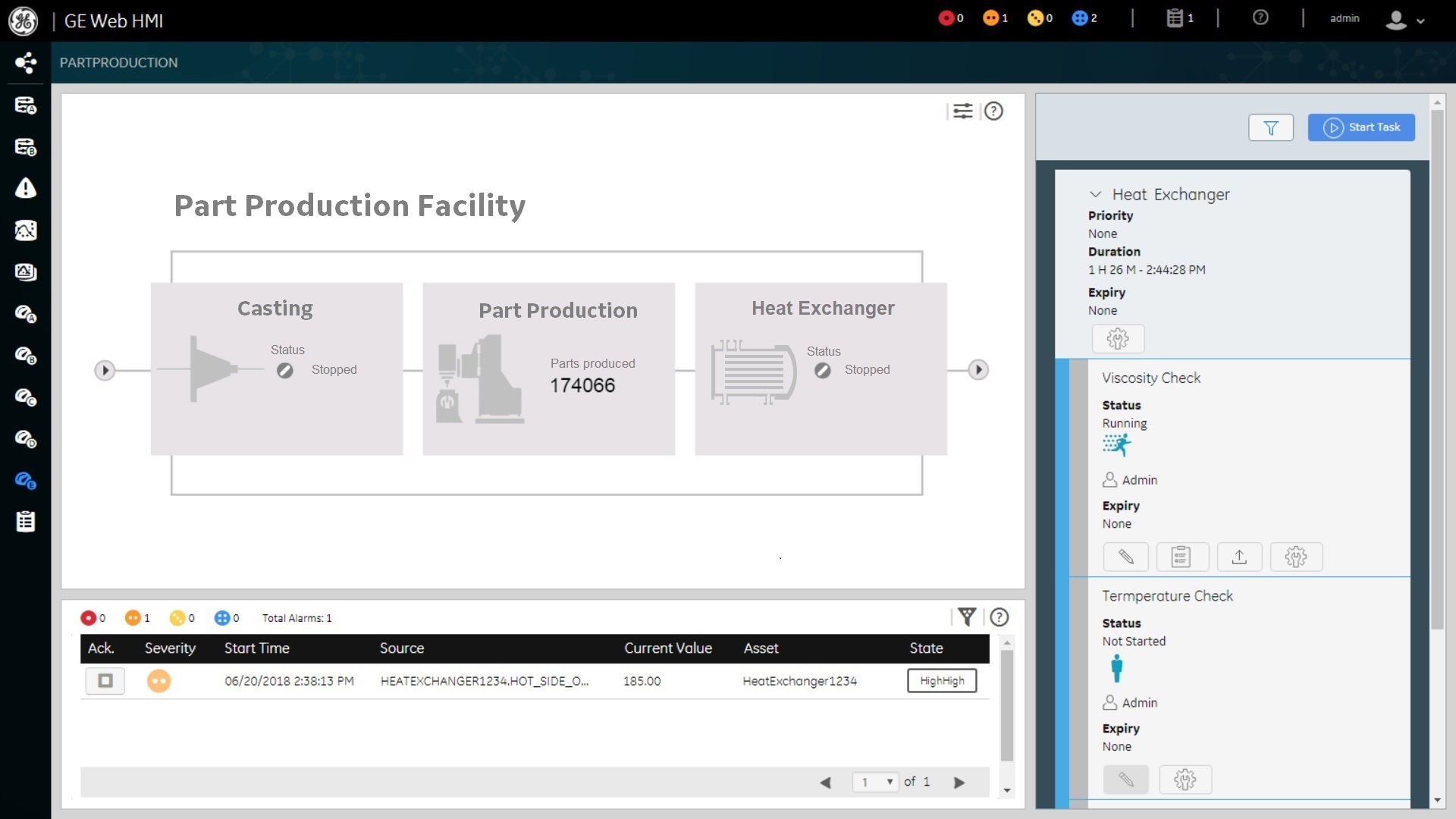 |
Today’s technology isn’t just about delivering the right information after an event has happened, it is also about delivering information before a catastrophic issue occurs and preventing it from taking place. |
Furthermore, fourth generation HMI/SCADA can add a layer of proactive analysis to deliver predictive intelligent alarming. Today’s technology isn’t just about delivering the right information after an event has happened, it is also about delivering information before a catastrophic issue occurs and preventing it from taking place.
Consider if a plant monitors a temperature, which exceeds the upper control limit and an alarm goes on. Traditionally, an operator would now react to the alarm. Analytics have made it possible to evolve from being reactionary to now predicting when the event will occur and taking proactive steps.
As an example, working with a food manufacturer, you can monitor the temperature data point, put an analytic on it and predict the temperature based on a statistical model. You can push an alarm to an operator to ensure that action is taken faster, before a batch is ruined.
This applies to other industries as well, such as pharmaceutical with multi-million-dollar batches of product, as well as maintenance events on discrete equipment. The application of predictive knowledge, delivered as an intelligent alarm, is far reaching across all industries and offers new possibilities for consistently optimized operations.
Alarms to the Right Person, at the Right Place–in Context
Furthermore, our IIoT world helps us send alarms in context. This means, once an alarm fires, an operator should be able to understand contextually, not just where in the plant the issue is occurring (from a location standpoint), but more directly, where and when in the processes they manage, there is an issue occurring.
Operators need to be able to understand the corrective action required to resolve an alarm. As such, seeing that alarm in context is important. In the past, operations teams relied on years of experience for that context – the so called “machine whisperer” who understood that if “x alarm” occurred under “y circumstances,” then it meant a conveyor, for example, was moving too fast and they knew exactly how to tweak a dial. With our changing workforce, those days are gone – and digitization must be the foundation for providing the context to newer, inexperienced workers.
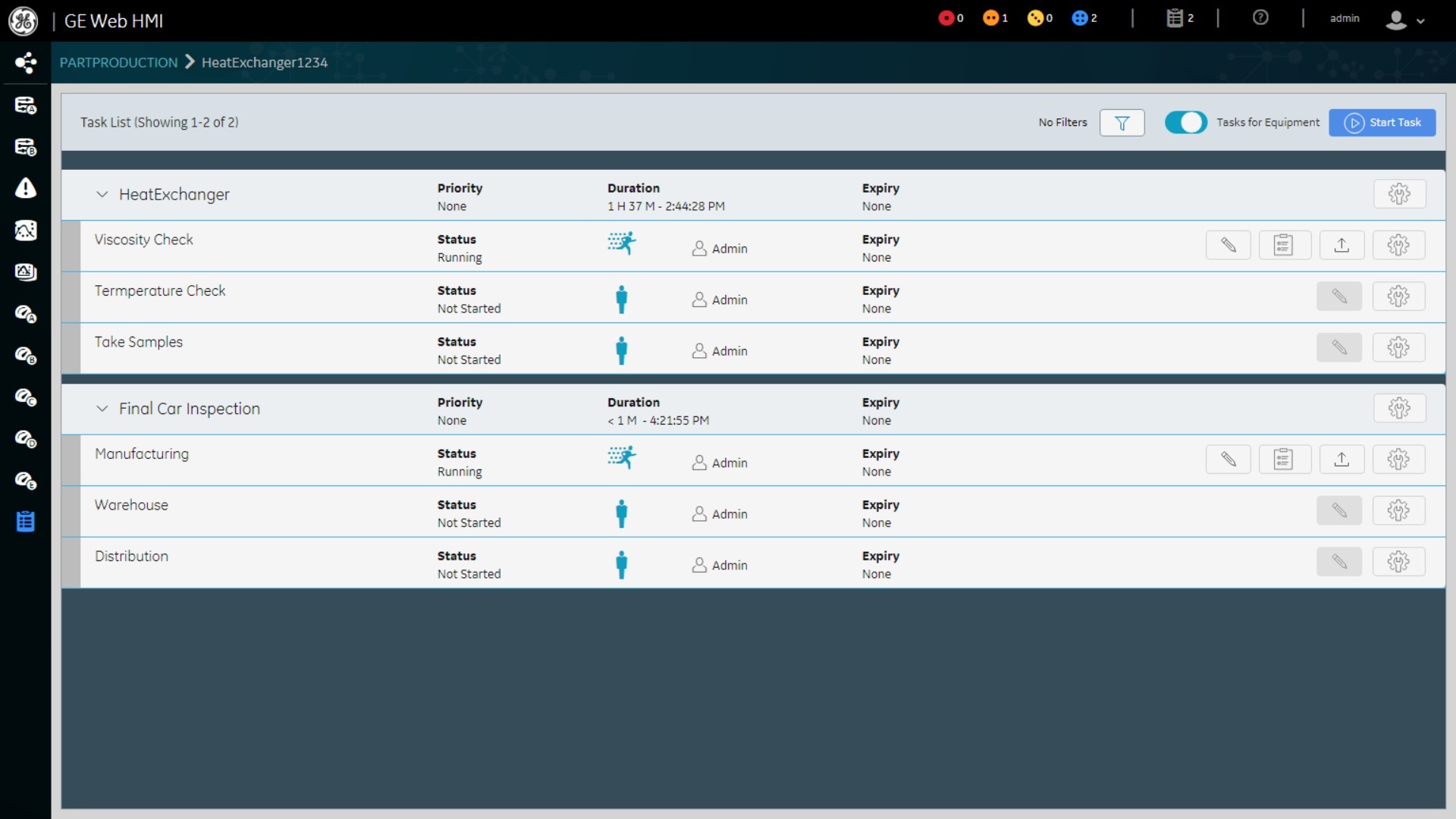 |
Control systems integrators can configure systems to deploy alarms and task instructions to an operator, engineer, or manager based on role and physical location.
|
Lastly, fourth generation HMI/SCADA gets the alarm, in context, to the right person in the right place. Control systems integrators can configure systems to deploy alarms to an operator, engineer, or manager based on role and physical location.
As an example, an engineer is standing on Floor 4 in front of a mixer and an alarm triggers related to a machine on Floor 1, which is 25 minutes away. Does it make sense to deploy the alarm to that engineer? Today’s HMI/SCADA system can determine that a colleague is standing 100 feet away from the machine in alarm – and instead send the signal to the closest engineer for faster, more efficient response.
The right information, in context, finds the right person in the right location, which is drastically different from the traditional SCADA world and drives faster action.
Smarter Operators with Intelligent Alarming
Today’s HMI/SCADA is not just monitoring and visualization, with alarms rolling in. For operators, HMI/SCADA is their Decision Support system, and intelligent alarm management is critical.
Here are two golden rules to think about:
- Don’t allow technology to complicate the operator experience.
- Use technology to improve the operator experience and manage alarms for greater efficiency.
With just a glance, operators should be able to recognize which information requires their attention and what it indicates. You can enable smarter operators with intelligent alarming for faster alarm detection, greater understanding, and improved business outcomes.
Take your customers’ operations to the next level with GE Digital’s proven HMI/SCADA solutions.